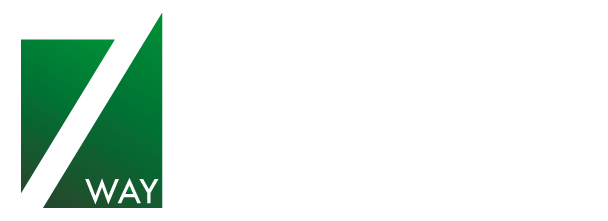
The role of droplet separators, demisters or mist eliminators is to remove a liquid from an air or gas flow using mechanical collection by surface or filaments. The liquid may be a pollutant or, like water, be per se benign, but in either case it is contaminating the air or gas.
The separation of the liquid from the air or gas within a process may:
-Prevent contamination of the process
-Prevent damage to, or corrosion of, downstream equipment
-Recover a useful product
-Prevent undesirable atmospheric emissions
The range of filter types
Liquid is entrained in an air or gas flow following either of 2 basic situations.
-The air or gas meeting mechanically generated spray or generating the spray as it passes through a liquid. Such mechanically formed sprays are termed ‘ droplets ‘ and are usually always over 5 to 10 microns in size. The coarser droplet filtration is done by impingement in a vane separator, and/ or by knitted wire demisters, also known as mesh pads.
-The air or gas reacts chemically or physically resulting in a fume or condensation mist formation. These particles are mist or aerosols mainly below 3 microns, frequently sub-micron in size. Fine droplet and mist filtration can be achieved using co-knitted wire / fibre coalescers or, for effective sub-micron collection, using Candle Filter type Mist Eliminators.
Mist Eliminators – often referred to as Candle Filters or Fibre Bed Filters – originally developed in the research laboratories of I.C.I. are intended for the complete removal of very fine mist particles less than 2 microns diameter.
The mechanism of Fibre Bed filters is well known and is basically a combination of impingement for particles greater than 1-2 microns in diameter and diffusion for the finer particles where Brownian motion becomes increasingly predominant.
As the gas passes through the filter bed the small mist particles are bombarded by the gas molecules surrounding them, causing them to move in various directions, towards and away from the surface of the fibres of the filter.
Brownian movement
Each filter is composed of millions of fibres and although the efficiency of each individual fibre is low the cumulative effect is very high. Low approach velocities are necessary in order not to mask the diffusion velocities associated with Brownian movement.
NON-WETTABLE FIBRE FILTERS
Experimental work has been carried out using glass fibres with differing surface properties and diameters, and with varying densities. A fibre was eventually discovered and a packing density established which exhibited a high efficiency.
It drained easily and produced an acceptable pressure loss. Research established that if the fibres were water repellent, bunching did not occur when mist passed through the bed. As the particles were collected on the fibres drop-wise, rather than film-wise, the fibres remained substantially dry.
The low approach velocity solution was the use of the so-called ‘candle’ filter involving preformed elements packed into a 5 centimeter annular space between two concentric cylinders fabricated from corrosion resistant mesh.
The candles are installed vertically and gases pass horizontally through the filter wall, the trapped particles coalescing and draining down through the filter bed. Gas flow through candles can be either inside/outside or outside/inside depending upon the siting of the installation and the method of securing the candles in place.
We can offer a range of filters to conform with the varying requirements of industry in terms of capacity, pressure loss and mist removal efficiency.
The technology offers Continuous high efficiency in separation efficiency and drainage. It is a designed for extreme conditions.
7 Way produces a variety of rigid oil mist filter housings easily to fit for every installation. To be located direct on top of oil tank or stand-alone aggregates for connection via external duct system.
Air flows: 100 m3/h to 6000 m3/h
Efficiency: Up to 100% @ ≥ 1 µm.
Auxiliaries:
*Differential pressure sensing transmitters.
*Differential gauges.
*Fan aggregates.
*Frequency converters for optimizing of flow and power consumption.
*Oil drainage.
*Service door.
Materials:
*Painted Carbon steel
*Stainless Steel
*Aluminium.
Static and carbon filters HVAC & industrial applications Dust and gas filtration
Electrical and liquid heaters HVAC & industrial applications for safe & ex areas
Vertical Vane filtration for air intakes & process water separations
Integrations for total functionality HVAC & industrial For safe & ex areas
For air and carbon filters HVAC & industrial applications Dust and gas filtration
Inovane inertial air filtration and water mist separators for your air intake solutions
To provide a good experience, we use technologies such as cookies to store and/or access device information. When you consent to these technologies, we may process data such as browsing behavior or unique identifiers on this website. If you do not consent or if you withdraw your consent, this may adversely affect certain features.